China’s Rare Earth Monopoly and the EV Challenge
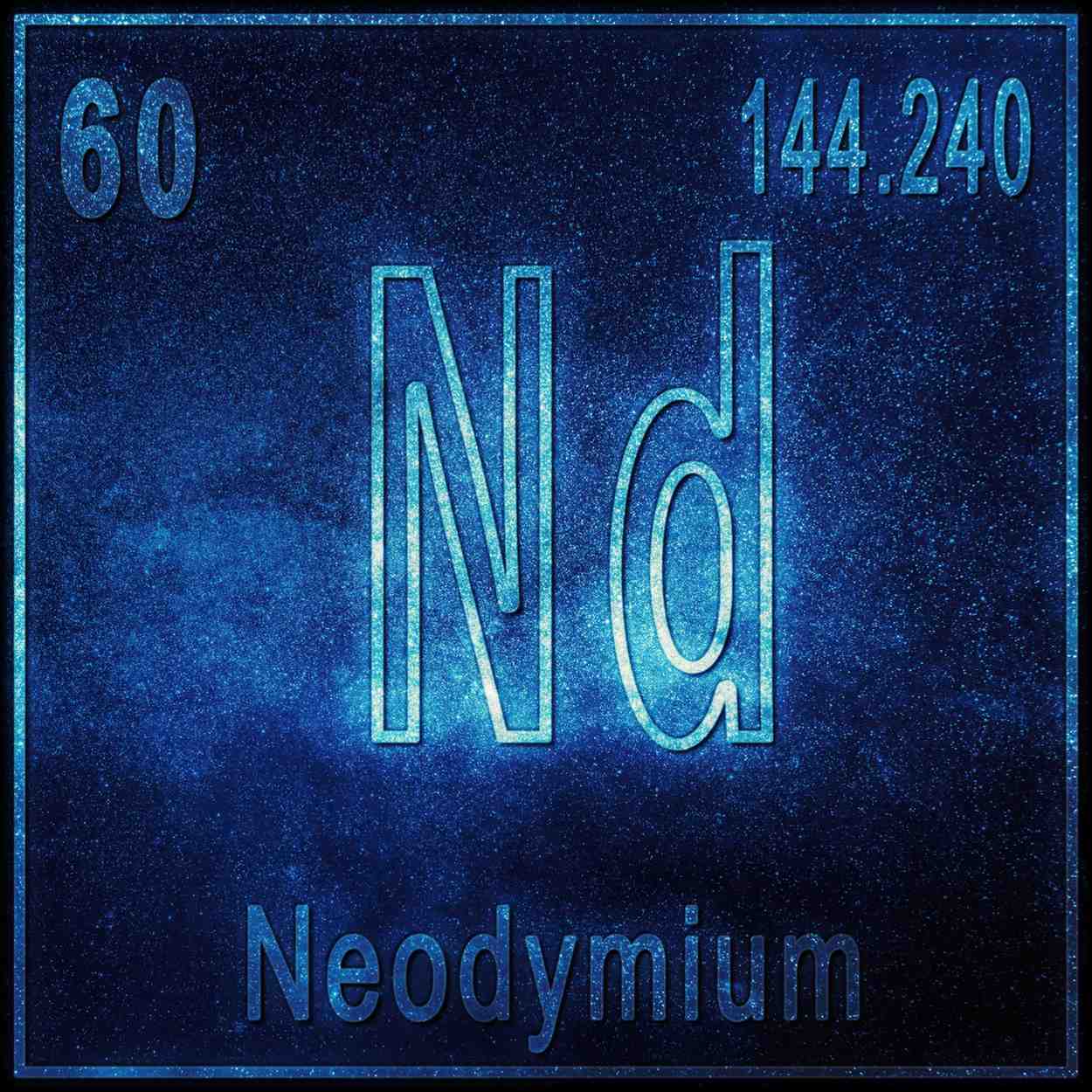
Under Pressure: China’s Rare Earth Curbs shake up the Automotive Scene
The global automotive industry is undergoing a profound transformation as China implements stricter controls on rare earth metal exports, which are essential for the production of electric vehicles (EVs), hybrid engines, and cutting-edge electronics. Currently, China holds a commanding position in the global rare earth supply chain, contributing over 60% of worldwide production and nearly 90% of processing capabilities. This significant dependence on a single nation for crucial materials such as neodymium, dysprosium, and praseodymium has emerged as a strategic vulnerability in the shift towards electrification and sustainable mobility.
Distribution of rare earths production worldwide by country, 2024
Source: Statista
Amid increasing geopolitical tensions and shifts in domestic policy, China's recent restrictions and tightening of export controls have raised alarm among automakers and governments alike. The consequences of these actions are particularly acute for EV manufacturers that heavily rely on rare earth permanent magnets for efficient electric motor performance. Such supply chain uncertainties are inflating material costs, delaying production timelines, and necessitating a reevaluation of sourcing and technological strategies across the industry.
In reaction to this crisis, the automotive sector is proactively exploring alternative approaches to lessen its reliance on Chinese rare earths. Various manufacturers are investing in rare earth-free motor technologies, such as induction motors, which are utilized by companies like Tesla in select models, and switched reluctance motors, both of which provide satisfactory performance without the need for rare earth elements. Concurrently, research efforts are intensifying around alternative magnetic materials such as manganese-bismuth (MnBi), ferrites, and iron nitride (FeN), which offer greater abundance and are less affected by geopolitical fluctuations.
Nations including the United States, Australia, and members of the European Union are also accelerating initiatives to establish domestic mining and refining infrastructures for rare earths, with the goal of diversifying the supply chain. The development of strategic partnerships, recycling programs, and circular economy frameworks is becoming increasingly prominent as automakers strive to reclaim rare earth elements from used batteries and end-of-life vehicles.
The rare earth supply challenge transcends mere supply chain concerns; it serves as a critical wake-up call for the automotive sector. It underscores the pressing necessity for technological innovation, geographical diversification, and sustainable sourcing practices within the industry. As the goal of achieving net-zero emissions rapidly approaches, the sector faces the complex task of navigating this intricate landscape while balancing growth with resilience. China's rare earth export restrictions have undoubtedly created turmoil in the industry, yet they have simultaneously spurred a strategic evolution that has the potential to reshape the future of automotive mobility.
Rerouting the Supply Chain: Auto Industry’s Backup Plan to China’s Rare Earth Grip
In response to China's restrictions on rare earth metal exports, the global community is implementing a multi-faceted approach aimed at reducing dependency on Chinese supply and enhancing the security of critical mineral supply chains. A primary strategy involves diversifying sources of rare earth minerals by developing new mining operations in countries such as Australia, Canada, the United States, Vietnam, and various African nations. Lynas Corporation from Australia has emerged as a significant non-Chinese supplier, while Vietnam is increasingly seen as a potential hub, bolstered by investments from Japanese and Korean firms. In conjunction with this, there is a concerted effort to establish independent refining and separation facilities outside of China, addressing the fact that the bulk of rare earth elements extracted worldwide are still being processed there. The U.S., EU, and Japan are actively investing in refining capabilities both domestically and in allied nations.
Another crucial element of this strategic shift is stockpiling rare earth minerals, akin to maintaining oil reserves, which can serve as a buffer against potential supply disruptions. Concurrently, countries are delving into the recycling of rare earth materials from electronic waste, with Japan and the EU leading initiatives in this area. There is also a growing focus on researching and developing alternative technologies, such as electric motors that do not depend on critical elements like neodymium or dysprosium. Additionally, global alliances are forming to enhance cooperation among nations, as exemplified by agreements like the U.S.-EU Critical Minerals Agreement and collaborative efforts among Quad nations, aimed at ensuring more stable and transparent supply chains.
Below table provides challenges and estimated success rate of magnet type compared to NdFeB:
Magnet Type |
Key Advantages |
Key Challenges |
Estimated Success Rate (%) vs NdFeB |
AlNiCo (Aluminum Nickel Cobalt) |
High remanence, excellent thermal stability |
Very poor coercivity, low energy product, expensive cobalt component |
20% |
SmCo (Samarium Cobalt) |
Good remanence, high coercivity, thermal stability |
Expensive, contains cobalt, lower energy product than NdFeB |
40% |
MnBi (Manganese Bismuth) |
Decent coercivity potential, no rare earths or cobalt |
Loses coercivity during manufacturing, low energy product |
30% |
Ferrites (e.g., FeN) |
Abundant, low-cost, better high-temp performance |
Very low energy product and magnetic strength, difficult to miniaturize |
25% |
Source: Academic Journals, Government and Lab Reports, Research Institutions and Industry
Governments are actively involvement through offering subsidies, grants, and facilitating public-private partnerships to support exploration, processing, and technological advancements within the rare earth sector. A strong emphasis is placed on environmentally and socially responsible mining practices, which are intended to attract investment while gaining public support. These practices ensure that environmental and social standards are maintained throughout the supply chain.
Altogether, these strategies not only seek to mitigate China's influence in the rare earth market but also aim to construct a more resilient, diversified, and ethical global supply chain for essential rare earth elements necessary for defense applications, electronics, renewable energy, and electric vehicles. Through collaboration and innovation, the focus is on creating a sustainable framework for the future of rare earth element sourcing and usage.